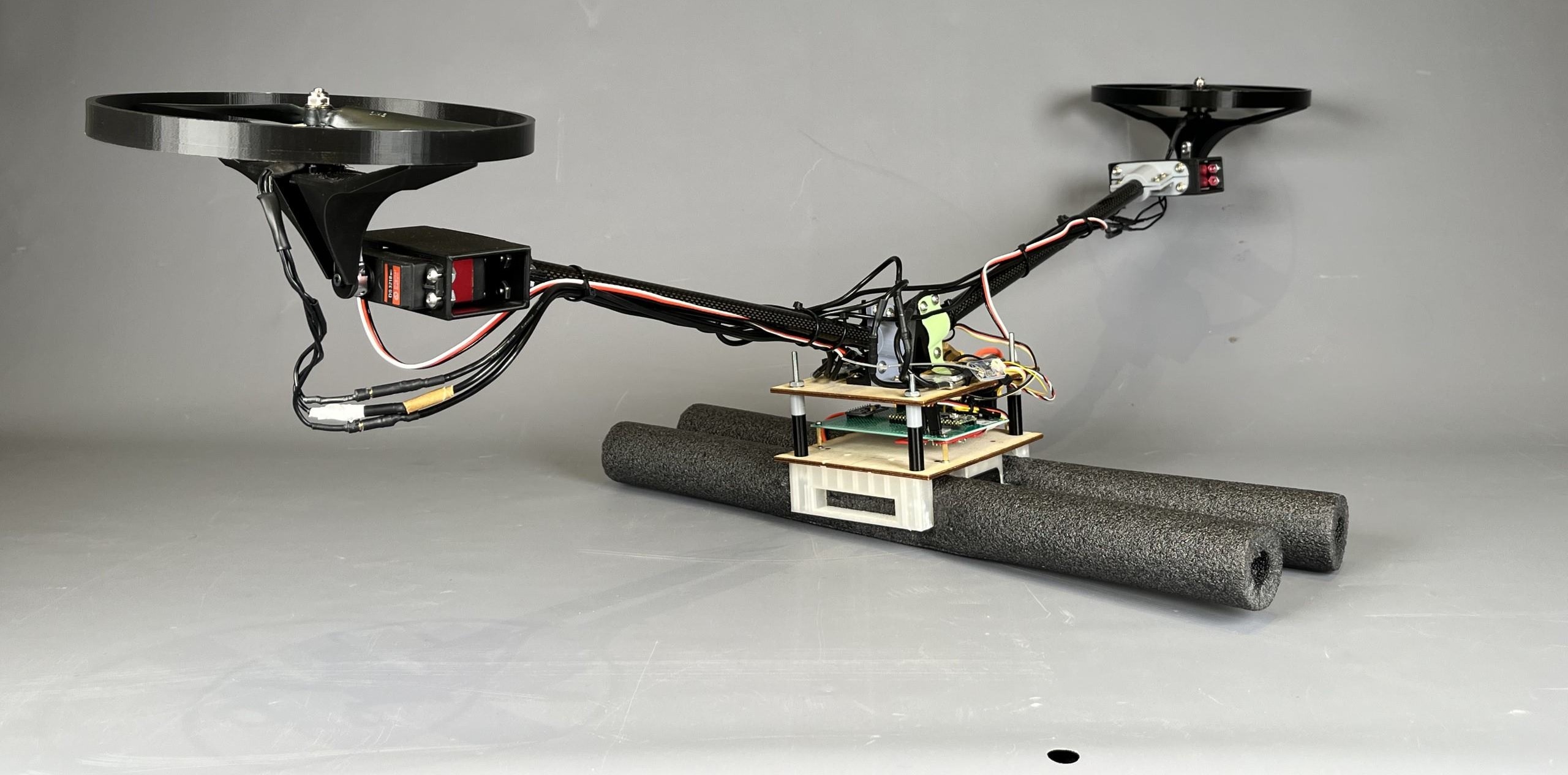
The priorities for this mechanical design were light weight, stiffness, and resilience. As a bicopter, the vehicle mounts a pair of drone motors to servos on PLA printed motor mounts, which connect the servo horn and the motors, with holes for machine screws and for the driveshaft to be able to rotate. These mounts are each designed with a built-in circular propeller guard which prevents damage to the aircraft on impact. As a testbed, protecting the most fragile parts of the aircraft, (propellers and electronics) is critical. The servos are likewise mounted in 3D printed PLA pods attached by clamps to carbon fiber tubes. The clamps are compressed onto the carbon fiber tubes with screws before attaching to the servo pods, to prevent sliding or rotation. The carbon fiber tubes balance stiffness with lightweight. Although the motors and propellers were chosen for maximum thrust, minimizing mass was still important, as we needed to add counterweights (in the form of extra screws taped to the airframe) for superior balance. The servos tilt the motors, changing the direction of thrust forces, to create pitch and yaw moments. Roll moments are created by changing the magnitude of thrust forces.
